Bag unloading, pneumatic transfer, and containment: a secure NFPA solution for military powders
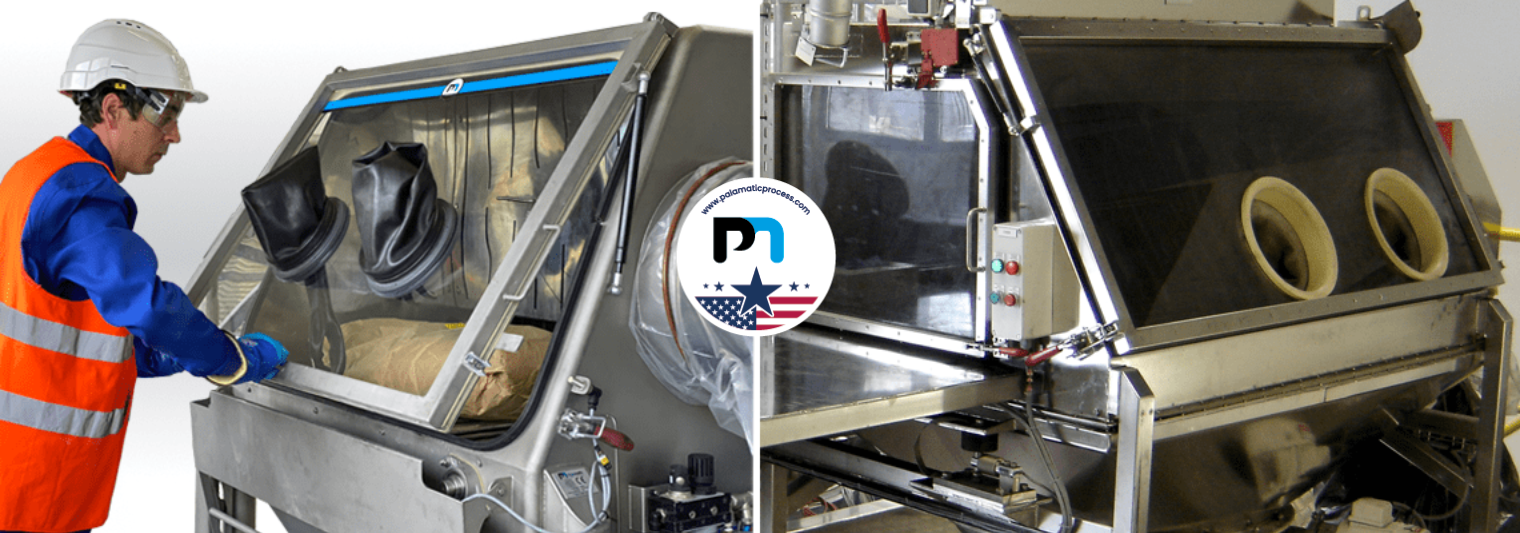
- 1. Understanding NFPA requirements for military powders
- 2. The confined bag emptying station: safety, ergonomics and performance
- 3. Pneumatic transfer: the ideal technology for explosive powders
- 4. A complete, modular, NFPA-certified industrial solution
- 5. Job integration: specific applications in the military sector
- 6. Conclusion
In the military sector, handling sensitive powders—whether explosive, pyrotechnic, or simply reactive—imposes extreme requirements in terms of safety, containment, and regulatory compliance. Even the slightest dispersion of dust into the ambient air can create an explosion hazard in NFPA zones, endangering both operators and facilities.
To address these challenges, a complete industrial solution integrating an NFPA bag discharge system, secure pneumatic transfer and absolute containment is required to meet the highest standards. This approach ensures reliable and repeatable handling of military powders, while guaranteeing traceability, cleanliness and process continuity.
Palamatic Process designs customized lines capable of integrating every stage of the material flow—from bag reception to final bagging—in a hermetic, filtered, and automated environment. This article presents the specific features of these systems, their compliance with NFPA standards, and their suitability for the most sensitive defense applications.
1. Understanding NFPA requirements for military powders
1.1 Objective: handling powders safely
In the military industry, handling sensitive powders—whether explosive, pyrotechnic, or simply reactive—imposes extreme safety requirements. These substances, often used in the manufacture of ammunition, explosives, or in propulsion processes, present a dual hazard: explosiveness and volatility. Handling them in bulk (during unloading, transfer, or dosing) exposes operators to the risk of deflagration, inhalation of toxic particles, and cross-contamination.
To meet these constraints, installations must comply with NFPA 2014/34/EU (equipment and protective systems intended for use in explosive atmospheres). These regulations require precise classification of zones (zone 20, 21 or 22) and equipment capable of preventing ignition sources, limiting the spread of an explosion or containing its effects.
1.2 NFPA classification: what are the constraints for equipment?
The NFPA regulations classify explosion-risk environments according to two main criteria:
- Class 2: concerns environments where combustible dust is present (to be distinguished from Class 1, which concerns gases and vapors).
- Each class is then divided into:
- Division 1: explosive dust is constant or frequent under normal operating conditions.
- Division 2: dust is occasional or unlikely, generally in the event of equipment failure or accidental leaks.
Each zone imposes specific requirements on materials, motors, sensors, emergency shutdown systems, and, above all, containment and filtration methods. A simple leak or source of static electricity can be enough to trigger an explosion. This is why all components—from the bag unloading station to the pneumatic transfer system—must be rigorously selected, NFPA certified, and installed in accordance with the standard.
1.3 What are the specific risks associated with pyrotechnic powders?
Powders used in military applications (nitrates, perchlorates, black powders, oxidizers, primers, etc.) have highly unstable physical and chemical properties. They can:
- Ignite spontaneously under the effect of simple friction or static electricity.
- Form highly explosive dust clouds suspended in the air.
- Chemically degrade on contact with moisture or ambient air, releasing toxic gases.
Simply spilling a bag can be enough to create a hazardous area if it is not properly contained. This is why an integrated system of containment, filtration, and grounding is absolutely necessary to dissipate electrostatic charges.
FAQ: What are the risks associated with handling powders in an NFPA environment?
The main risks are:
- Explosion due to a concentration of flammable dust in the air,
- Ignition by a spark (electrostatic, mechanical, or thermal),
- Contamination of operators through inhalation of toxic particles.
In an NFPA environment, these risks are multiplied by process constraints (unpacking, transfer, dosing), requiring rigorous equipment design to ensure the safety of people and facilities.
2. The confined bag emptying station: safety, ergonomics and performance
2.1 Objective: to ensure dust-free unloading
In the military sector, manual deconditioning of sensitive powders is a critical phase of the process. Simply opening a bag of pyrotechnic powder can release fine particles that are dangerous to both operators and the working environment. There is a real risk of explosive dust clouds forming, particularly when unloading multi-layer paper bags or bags containing hygroscopic materials.
The objective is therefore clear: to open, empty and dispose of bags without ever exposing the product to the ambient air, while ensuring a healthy, safe working environment that complies with NFPA guidelines.
2.2 How a Sacktip® SE station works in an explosive environment
The Palamatic Process Sacktip® SE station is specially designed to meet the most stringent safety standards, particularly for explosive or reactive powders. Its principle is based on a confined, sealed enclosure equipped with a glove box, allowing the operator to handle the bag without ever coming into contact with the powder.
Here are the key steps in its operation:
- The bag is inserted from the side through a secure, sealed hatch.
- The bag is opened under containment, with the bag held in position.
- Controlled unloading into a hopper connected to a transfer or dosing system.
- Automatic evacuation of the empty bag to a compactor or collector, without manual removal.
- Continuous dust extraction, integrated into the cabin, with H13 or H14 rated filter cartridges.
The structure can be made entirely of 304L or 316L stainless steel, with mirror-finished interiors to ensure hygiene and product flow without retention. All critical components (fans, sensors, motors) are NFPA certified according to their location.
2.3 Containment options: glove box, H14 filter, integrated dust extraction
Each unloading station can be customized according to the level of containment required:
- Glove box, single or double station, for contactless operator intervention.
- H14 absolute filtration with automatic cleaning, for fine dust capture.
- Dust removal ring, ensuring continuous extraction of fine particles during unloading.
- Bag connection with internal liner, reinforced sealing and hermetic welding.
- Contactless foot pedal to activate the unloading cycle without risk.
Palamatic also offers the integration of an integrated bag compactor into the containment enclosure, avoiding any handling of contaminated empty bags outside the cabin.
FAQ: What is a bag discharge system for explosive areas?
An NFPA bag discharge system is a piece of equipment designed to enable the safe opening and unloading of bags containing potentially explosive powders. It is contained, sealed, equipped with explosion-proof filters and designed to prevent any source of ignition (static electricity, mechanical heating, sparks). It protects operators and the working environment and prevents the risk of explosion from airborne dust.
3. Pneumatic transfer: the ideal technology for explosive powders
3.1 Objective: transport powder without breaking containment
In a facility classified according to NFPA guidelines for military powders, the transfer of product between two pieces of equipment (for example, from the unloading station to the dosing or filling system) is a critical step. This transfer must be carried out without loss of containment, without product accumulation, and without friction that could create a source of ignition.
Pneumatic transfer is the optimal solution for moving explosive powders, as it allows for completely sealed conveying without manual intervention or mechanical chain or screw transport, which often generate too much kinetic energy or heat.
3.2 Choose between dilute or dense transfer depending on the military powders
There are two main principles of pneumatic transfer using positive or negative pressure:
- Diluted transfer: the product is conveyed at high speed in a fast, continuous air flow. This mode is effective for light powders but can generate abrasion or static electricity. It is therefore not recommended for pyrotechnic or fragile powders.
- Dense transfer: the product is pushed in bursts through a low-speed, high-concentration air stream. This mode reduces friction, dust cloud formation, and electrostatic risks. It is ideal for explosive, unstable, or hygroscopic powders.
At Palamatic Process, dense pneumatic transfer is preferred for these sensitive applications. It is often equipped with antistatic sleeve valves, 316L stainless steel lines with internal treatment, differential pressure sensors and grounding points.
3.3 Integration of a secure transfer circuit with terminal filtration
A complete pneumatic transfer system for military powders generally includes:
- A confined unloading station or buffer hopper,
- A pneumatic injector or NFPA rotary valve,
- A network of antistatic stainless steel pipes with long-reach elbows,
- An absolute terminal filter, often class H14, with explosion-proof cartridges,
- Pressure switches, non-return valves, and secure purge systems.
The entire system is controlled by a Pal'Touch® controller, which manages the transfer sequences according to weight, time, or pressure criteria, ensuring both performance and traceability.
Finally, maintenance is simplified thanks to Easyclean systems for quick disassembly of transfer lines and thorough cleaning between sensitive batches.
FAQ: What is the difference between dilute and dense pneumatic transfer?
Diluted pneumatic transfer uses a fast air flow to transport low-concentration powders, ideal for less sensitive products. Conversely, dense transfer transports the product slowly, in packets, with little air and less turbulence. This method is preferred for explosive or sensitive powders, as it limits wear on the pipes, the generation of static electricity, and the risk of explosion.
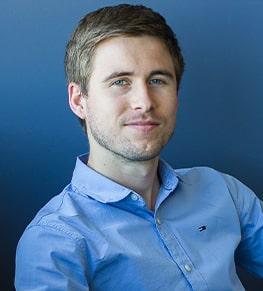
Do you have a project involving the transfer of explosive powders in an ATEX environment ?
I am available to assist you.
Guillaume, expert in explosion-proof powder transfer systems
4. A complete, modular and NFPA-certified industrial solution
4.1 Objective: integrate all stages of the process into a single secure line
Handling explosive powders in a military environment leaves no room for improvisation. To guarantee operator safety, regulatory compliance and production performance, it is essential to integrate every stage of the process—from bag reception to filling—into a unified, controlled, and secure system.
An effective solution does not rely solely on the addition of independent equipment, but on a complete line designed in a modular fashion where each module (emptying, transfer, dosing, filling, dust extraction) is perfectly interconnected, adapted to the NFPA environment, and designed to work in synergy.
4.2 Connection between emptying, transfer, and weight dosing
In a standard Palamatic Process configuration, the equipment is linked as follows:
- Contained bag emptying (Sacktip® SE): controlled opening without dust emissions.
- NFPA buffer hopper with vibrating bottom or mechanical de-duster to ensure smooth flow of sensitive powders.
- Dense pneumatic transfer system to a dosing or filling station.
- Weighing feeder (screw or belt) for precise control of the quantity transferred.
- Safe filling (bags, drums, big bags) with weighing, containment and dust management.
Each transition point is equipped with flexible antistatic sleeves, expanding seals for tightness, and connected sensors for real-time process monitoring.
4.3 Automation, weighing, traceability: the contribution of Palamatic Process solutions
Centralized control via the Pal'Touch® interface allows intuitive management of:
- transfer parameters (time, flow rate, pressure),
- traceability of operations (weight unloaded, batch number, operator, etc.),
- safety alerts (clogging, excessive pressure, NFPA fault).
The automation system can include:
- customized product recipes (by powder, by process),
- valve and flap management,
- integration into a MES or ERP system for complete synchronization of the production line.
The result: a faster, safer system with no risk of human error, compliant with the quality requirements of the defense sector.
FAQ: How does an integrated dust extraction system work?
An integrated dust extraction system captures fine particles released during the emptying, transfer or filling of powders. It consists of filter cartridges (often H13 or H14), an automatic cleaning system (using compressed air), an NFPA fan, and a collection chamber. The filtered air can be exhausted or recycled, and the system is designed to operate in negative pressure to ensure total containment of the installation.
5. Job integration: specific applications in the military sector
5.1 Objectif : répondre aux contraintes des poudres pyrotechniques et sensibles
Le traitement des poudres dans le domaine militaire ne se limite pas à une question de performance ou d’automatisation. Il s’agit d’un enjeu de sécurité nationale, où la moindre erreur peut avoir des conséquences dramatiques. Les poudres manipulées – propulseurs, amorces, charges explosives, additifs chimiques réactifs – présentent des propriétés hautement instables, que ce soit par leur sensibilité à la friction, leur hygroscopicité ou leur toxicité.
Les installations doivent donc :
- Être certifiées NFPA zone 20/21 sur toute la chaîne (intérieur des équipements et enveloppes extérieures).
- Garantir une manutention sans émission, en environnement confiné.
- Assurer une traçabilité complète des lots manipulés.
- Offrir des solutions de nettoyage rapide et sécurisé entre deux séries (changement de poudre, changement de recette).
5.2 Cas d’usage : ligne de remplissage sécurisée pour poudre d’amorce
Prenons l’exemple d’une ligne de traitement pour la poudre d’amorce utilisée dans la fabrication de détonateurs :
- Réception de la poudre dans des sacs unitaires, stockés en zone NFPA avec contrôle hygrométrique.
- Vidange manuelle confinée via une station Sacktip® SE avec boîte à gants.
- Transfert pneumatique dense avec mise à la terre à chaque point de connexion.
- Tamisage de sécurité en ligne pour éliminer les agglomérats.
- Doseur pondéral haute précision pour le remplissage contrôlé de mini-contenants.
- Poste de remplissage semi-automatique avec fermeture et scellage du produit.
Cette configuration limite drastiquement l’exposition de l’opérateur, évite les pertes de produit, sécurise la production, et répond aux exigences de l’armée en matière de sûreté, répétabilité et hygiène de production.
5.3 Maintenance, nettoyage, ergonomie : les atouts d’une conception sur mesure
Contrairement aux installations standard, les lignes NFPA pour poudres militaires doivent intégrer :
- Des systèmes de démontage rapide (Easyclean, connexions clamp, trappes de visite),
- Des zones de maintenance à distance, pour éviter toute intervention directe en zone à risque,
- Une structure modulaire, permettant d’isoler un équipement sans arrêter toute la ligne,
- Un nettoyage en place (NEP) ou à sec, selon la sensibilité des poudres,
- Une ergonomie pensée pour l’opérateur, avec accès par panneaux latéraux, commandes sans contact, écrans intuitifs.
L’objectif n’est pas seulement de répondre aux normes, mais de concevoir un environnement de travail sécurisé, fluide, reproductible et adapté aux contraintes humaines du terrain.
FAQ : Quels équipements industriels pour les poudres sensibles dans le secteur militaire ?
Les équipements recommandés sont :
- Stations de vidange confinées avec boîte à gants (Sacktip® SE),
- Systèmes de transfert pneumatique dense en inox antistatique,
- Doseurs pondéraux à vis avec confinement et traçabilité,
- Postes de remplissage (sacs, fûts, contenants spécifiques) en environnement NFPA,
- Systèmes de dépoussiérage filtrant (cartouches H14),
- Interface de supervision (Pal’Touch®) avec recettes, traçabilité, gestion des alarmes.
Tous ces éléments doivent être certifiés pour zones NFPA 20 ou 21 selon leur implantation, et configurables pour répondre aux spécificités des poudres explosives, hygroscopiques ou toxiques.
6. Conclusion
In the military industry, safety is non-negotiable. Handling explosive or pyrotechnic powders requires absolute rigor at every stage: from receipt of raw materials to final packaging. A compartmentalized approach with isolated equipment is no longer sufficient. Only a comprehensive solution designed for containment, secure transfer, and NFPA compliance can meet the real challenges in the field.
Palamatic Process designs and integrates complete customized lines, combining:
- Contained emptying stations,
- Dense pneumatic transfer,
- Weight dosing,
- Filling under controlled atmosphere,
- H14 dust extraction,
- Centralized control.
These installations are certified, proven, and already in operation in several sensitive contexts related to defense and critical powders. They guarantee operator safety, process reliability, and regulatory compliance.