Processed powder: infant milk powder
Milk powder mixing line
The customer is a manufacturer of infant milk powder.
Objective: preparation of the mix based on specific ingredients according to market demands and targeted segments: infant milk, second age milk and growth formulas. The composition of infant milk can vary depending on the additions and required doses of specific powders. These powders can change according to the ingredients such as: proteins, DHA fatty acid, vitamins, etc.
The mixing line is designed for complete cleaning with the dismantling features of the equipment via our Palamatic EasyClean range.
This infant mixing line is made up of a sack and bulk bag deconditioning unit for the loading of powders. The general design is implemented in a mixing tower stack up for a gravity-based operation. The entire pneumatic conveying system design provides minimum product retention to facilitate cleaning and ensure the overall hygiene of the mixing tower.
Under the sack discharge station a safety vibrating sieve and rotating magnet provide quality control in the gravity feed of the double-shaft mixer. The bulk bag unloading station is connected to the horizontal mixer via a flexible BFM fitting sleeve to permit a weight in loss operation into the mixer.
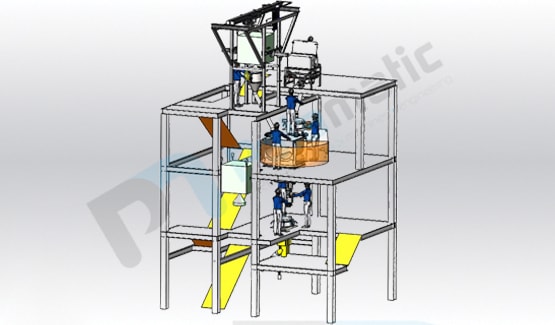
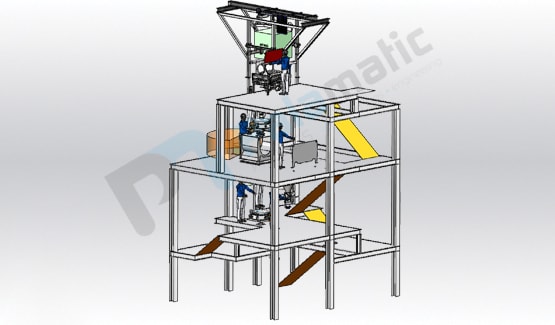
To provide consistencies in reproducing recipes, each "level" of equipment includes integrated features in the overall design. The bulk bag discharge station is set up on load cells as well as the sack tip tray station. All materials fed into the mixing line are weighed and scanned for total control and traceability. The design of the automation program meets the global strategy of food safety: suggest / authorize / check. For example, the automaton informs the operator about the material to be loaded and authorizes the opening of the door which begins the loading of the contents through a piloted lock. The automaton, via the scales, makes sure that the weight introduced is correct and the scanned code corresponds to the requested material. The mixer is also weighed, which makes it possible to cross-check the information from the sack dump station and the bulk bag unloader.The packaging line, installed at the mixer outlet via a hygienic buffer hopper, ensures continuity of production despite the batch function of the upstream line.
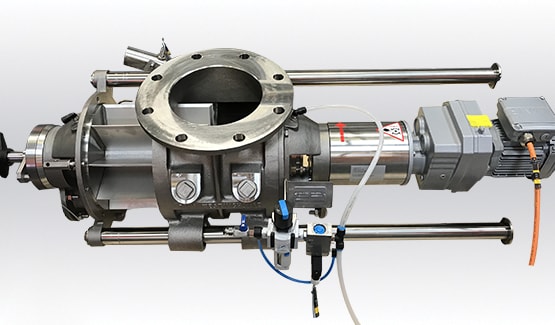
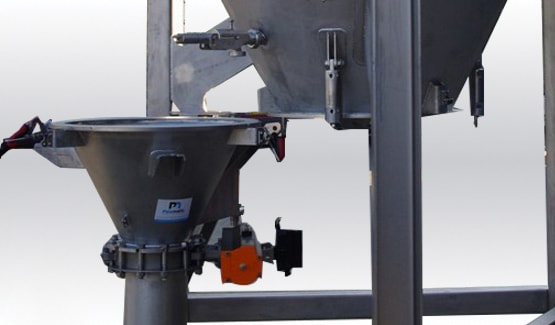
The cleaning of powder handling equipment is carried out by dismantling and accessing the heart of the system. Dry cleaning methods meet the hygienic requirements for this installation. The total open profile design of the equipment prohibits any retention of powders and gives full access for cleaning. Guide rails enable the agitator shafts to be removed from the mixer, access to the sieve grid (magnetic grid), access to the bottom of the buffer hopper as well as access to the rotary lock valve casing.
The platform permits access to all of the equipment by the semi-level installation. This platform designed and manufactured by Palamatic Process is made to meet all project constraints: integration in the customer building, hygiene, easy access to all equipment, heavy load support (1 ton big bag), rigidity for reliability and weighing accuracy.
Entirely designed in stainless steel, this mixing line for infant milk ensures a rate of 1.2 t./h with severe hygienic features and continuous feeding of the lid box line.