Mixing line for fragile dry ingredients
The DryBulk-Mix® line is dedicated to manufacturers of natural ingredients mixtures, such as: dried fruits, cereals, teas, potpourri, herbs, seasonings, etc.
The need to clean the manufacturing equipment in short time, as well as respect for the product integrity are ensured by the technological choices of this production line (e.g., vibrating dosing, belt conveyor, tilting bucket conveyor and "soft" mixer).
- No material attrition (gentle handling)
- Hygienic design
- Accurate ingredient dosing
- Installation flexibility
Models
DryBulk-Mix® stat | DryBulk-Mix® rota | |
---|---|---|
Number of dosed ingredients | 2 / 4 / 6 / 8 | 2 / 4 / 6 / 8 |
Production capacity | From 200 kg/hr to 8,000 kg/hr | From 200 kg/hr to 8,000 kg/hr |
Transfer technology | Belt conveyor | Tipping bucket conveyor |
Mixer type | Static mixer | Rotary tank mixer |
Reconditioning | Bulk bag or packaging machine | Big bag or packaging machine |
Loading and dosing
The DryBulk-Mix® line assures the dosing of various dried fruits (nuts, coconut, raisins, etc.), cereals (nuggets, muesli, dried fruits, etc.) and ingredients for feeding the soft mixer.
The dosing of the bulk ingredients is conducted by a vibrating feeder and load cells to obtain a precise mixture recipe. The production recipe controls the dosing of the vibrating corridors via the automatic control. Each product is stored in a dedicated buffer hopper with an independent weighing chain.
The dedicated hoppers are fed from sacks or bulk bags.
Transfer / Feeding
The transfer of fragile ingredients is conducted by a bucket elevator or belt conveyor. These two options prevent product attrition so the integrity of the recipe is kept intact.
Conveyor belt or tilting bucket elevator: what to choose?
Depending on your manufacturing constraints and the size of your production batches, Palamatic Process experts will advise you on the optimal choice.
Tipping bucket elevators provide elevation conveying for great heights with a small footprint!
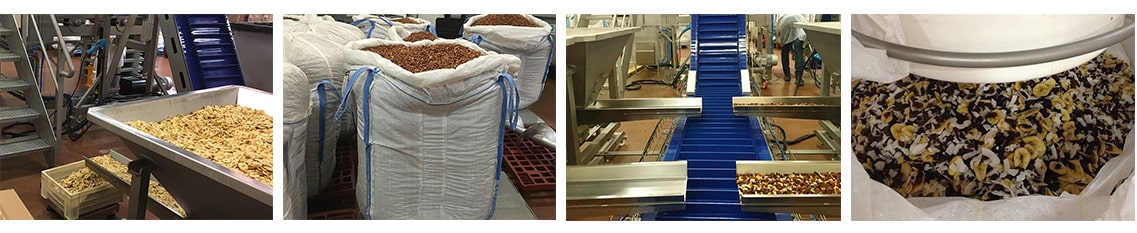
Mixing: two possible technologies
The mixer ensures the homogeneity of the recipe without breaking the products via its gentle action.
The technologies available are: low speed paddle mixer or rotary tank mixer / rotating tank mixer.
The volume range of the mixer is 70 liters up to 2,500 liters.
Just like the stirred arm mixer, the rotary tank / rotating tank mixer also allows the incorporation of liquid to spray aroma or oil on the recipe in production.

Mixer / conditioning outlet
On leaving the mixer, repackaging is carried out in a bulk bag for internal use for the purpose of future repackaging to 25 – 50 lb. sacks and/or boxes.
The bulk bag is filled by a FlowMatic® 03 Care station, allowing products to be weighed and drop height support.
When the mixer is directly upstream of the bag packaging machine, a tilting bucket elevator supplies the feed of the product. The integrity of the product and recipe are protected, and the footprint is kept to a minimum via a vertical installation (gravity process).
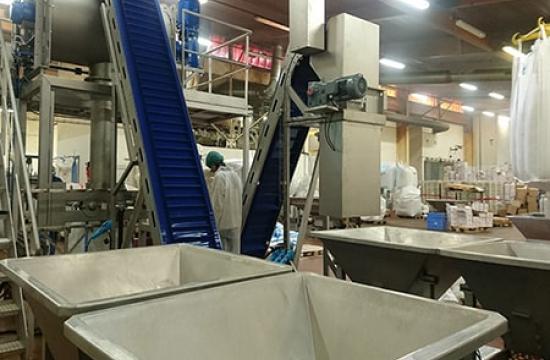
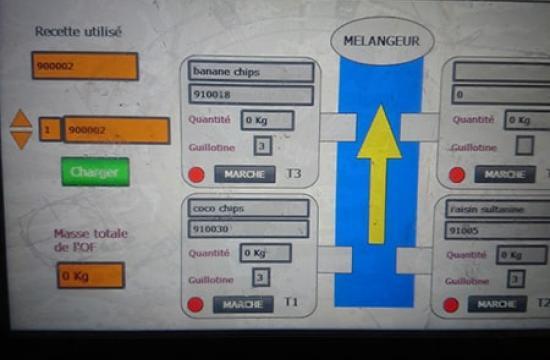
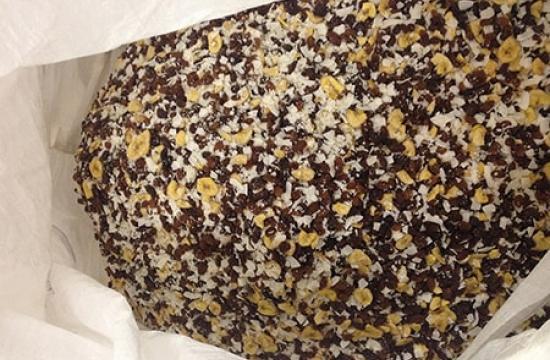
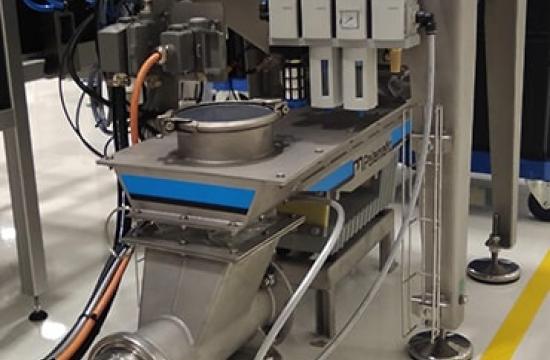
Learn about our customers' installations of the DryBulk-Mix® dry and fragile ingredient mixing line.
All the equipment integrated in the process line for mixing fragile dry ingredients is available below.