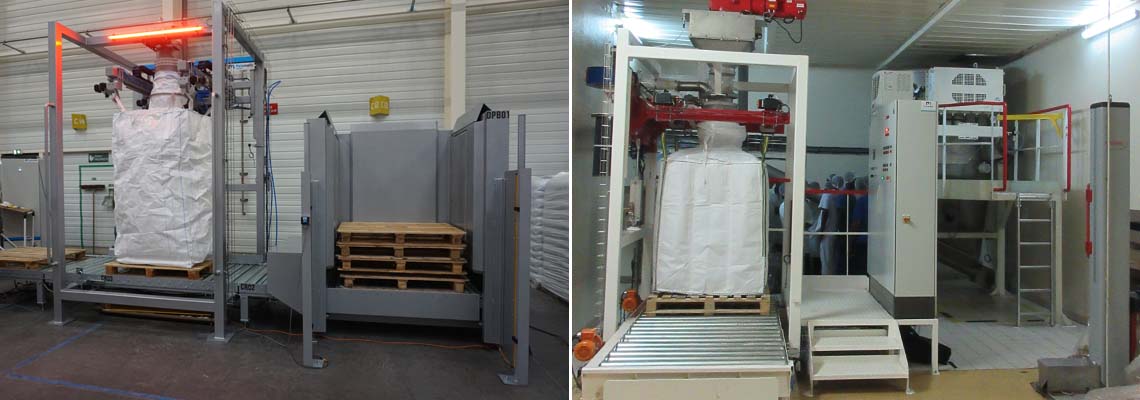
There is no doubt that bulk bags (also called super sacks, jumbo bags, big bags and FIBCs) have become the preferred choice of packaging for dry bulk materials.
They provide an easy and cost-effective solution for the storage and transport of materials to various industries and markets around the world. It is important to have easy to use solutions for the packaging of raw materials and finished products when dealing with bulk bags. There is a wide variety of equipment solutions to choose from for bulk material loading operations. Over the past several decades, production facilities have shifted more towards full plant automation. The growth in automation is happening for a variety of reasons, minimizing the need for human operators, improving workplace safety and ergonomics and increasing production capacity.
1. Minimize operator intervention
The global manufacturing market has seen an increase in competition from countries all over the world. Because of this, manufacturer’s need to examine every aspect of input costs and overhead to stay competitive. In recent years, all industries have seen more issues with labor shortages that have put a strain on their production capabilities. The need for automated systems in production plants is in higher demand as manufacturers face increasing economic pressure. Bulk bag filling systems can be designed to run with a negligible amount of operator supervision. Some designs incorporate elements such as automated feeding of empty bulk bags onto a filling station, while others may require an operator to place an empty bulk bag on the filling spout and handle hooks.
Other elements such as pallet unstackers and motorized roller conveyors can transfer a pallet to the filling station automatically. Once in place, and with the bag secured on the filling head, the PLC can guide the rest of the operation via load cells and level sensors. Once the big bag is full, the conveyor transfers it to a buffer area so a forklift operator can take it to storage for final transport. However, it is also possible to design a network of roller conveyors with turntables to help steer and guide the freshly packed super sacks to the appropriate destination within the plant.
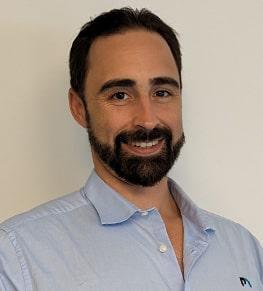
Do you have a project? I am available to
advise you and accompany you in your study.
Tarik, powder expert
2. Ergonomics and Safety
Palamatic Process has designed automated bulk bag filling systems with operational ergonomics and safety as a top priority. By creating a system of programmable sequences to automate the powder filling process, operators have little involvement and therefore a greater reduction in risk of injury.
All the heavy lifting is carried out by the system; loading and transfer of the pallet, filling and weighing, automatic release, transfer of the filled bulk bag to buffer area, etc.
The only involvement required by an operator is the placement of the empty bulk bag on the filling station. The operator attaches the filling spout to the inflatable seal and the handles to the automatic release hooks. Further design elements can be integrated such as: automatic closing and sealing of the fill spout, safety cages around moving parts, grounding of the equipment, hazardous area ratings on electrical components and conveyor turntables for re-direction of filled super sacks.
3. Increased production
With traditional bulk bag fillers, operators must spend a good portion of their shift loading, filling, unloading and moving bulk bags weighing anywhere between 1 to 2 tons each. This process can be slow and tedious, often resulting in 6-8 bulk bags per hour of production.
This is not the best rate when end market demand requires an increase in production and delivery of materials. By automating your production process, the filling sequence can work in masked time. In other words, while one bag is being filled, the next bag and pallet is being prepared by the system. Once the bulk bag is released by the automated hooks, the next bag and pellet is ready to be loaded. Palamatic Process offers the “Flowmatic® 04” automated bulk bag filling system, that in some applications can achieve filling rates of 30+ bulk bags per hour. This heavy-duty bulk material handling equipment can be used in the most difficult of material unloading operations.
Since 1992, Palamatic Process has provided equipment to over 2000+ installations in over 30 countries. We offer knowledge and expertise in all manner of powder and bulk automated material handling needs. Examples include, conveyor systems: pneumatic or mechanical, pallet conveying, screw conveyors, roller conveyors, turnkey solutions, material flow devices, food-grade design, bulk bag equipment, etc.
Contact one of our experts today for assistance with needed material handling solutions and to request a quote.
