Dedicated mixing line for dry materials
The gravity mixing line dedicated to materials requiring strict hygienic requirements, is designed to meet the needs of manufacturers in the infant formula food, pharmaceuticals and high value products industries.
The compact design ensures installation in a horizontally restrictive area but does require a height clearance of around 33 feet.
All of the integrated support equipment meets the hygienic requirements and typical cleaning procedures related to the most arduous of applications.
- Hygienic design and easy cleaning
- Gravity solution = reduced need for installation of support equipment
- Quality mixing
- Control and monitoring of quantities by industrial IT
The center piece of this processing line is a vertical mixer specially designed for demanding applications in terms of quality and cleaning.
Models
DryMixFlow® 500 | DryMixFlow® 1 000 | DryMixFlow® 1 500 | |
---|---|---|---|
Line speed | 500 Kg/h | 2,000 Kg/h | 3,000 Kg/h |
Mixer type | 1 vertical shaft | 2 vertical shafts | 2 vertical shafts |
Number of empty bags | 1 | 2 | 2 |
Number of empty bulk bags | 1 | 1 | 1 |
Number of sieves | 2 | 3 | 3 |
Magnetic detection | 1 | 1 | 1 |
Row height (approx.) | 39 ft | 41 ft | 41 ft |
Puissance électrique | 12.5 | 17 | 22 |
Gravity
The formulation line is a vertical integration where material transfers are provided by gravity, which avoids the installation of screws or pneumatic systems. The vertical mixing line integrates only functional equipment: unloading, sieving, mixing, DPM, packaging, which provides optimal efficiency!
The VTM mixer at the core of the system
The Palamatic Process VTM vertical mixer offers the best compromise between mixing quality, mixing cycle time and ease of cleaning. Its vertical design offers minimal product retention and the scraper blade ensures the sequence of production batches.
Depending on the complexity of the mixes produced, the cycle time is between 3 and 10 minutes. The introduction of liquid into mixtures is possible with additional dispersers (choppers) providing the homogeneity of the mixed materials. The volume of the mixer tank varies between 500 and 1,500 liters depending on the desired production capacity of the line.
Hygiene
The vertically designed VTM mixer allows minimal retention compared to other types of mixers, but also prevents product from coming into contact with the shaft bearing. The stirring wheel is partially maintained from above the mixer, which is why there is no contact with the product. However, inert gases can be injected through this seal if required.
Other equipment is not left out since all hoppers are removable for easy access to inspect or clean the equipment.
The hygienically designed sieve is equipped with a special articulation allowing the dismantling of the screens by a single operator.
CIP washing nozzles complete the hygienic system of this mixing line.
Control of the line
Automation and industrial computing play a major role in the management of mixing recipes. The identification of ingredients, and also of the operator, is an essential function to guarantee a high-quality end product. The traceability of the batch and the recording of the recipe / weight introduced ensures control of product quality. The touch screens positioned at the operator station provides ergonomics for operating the line.
Which products and which ingredients are processed?
Infant formulas are complex and have special requirements. Palamatic's DryMixFlow® lines, installed with our customers in the baby food industry, guarantee the production of vitamin powdered milk and medicated milk powder. These atomized milk powders are generally enriched with proteins, lactose and/or glucose, maltodextrin, vitamins (B1, B3, B5, B6, B9, C, D, E), minerals (sodium, magnesium, calcium, iron, zinc, copper, potassium, manganese) and amino acids (arginine, histidine, taurine, carnitine).
Manufacturers of instant drinks also use the DryMixFlow® lines for the production of their premix goods. There are many mixed ingredients:
- Sugar in the forms of maltodextrin, glucose, fructose, sucrose and specific powder supplements
- Mineral salts: potassium, sodium, magnesium, etc.
- Vitamins, mainly of group B, C and E.
- Amino acids
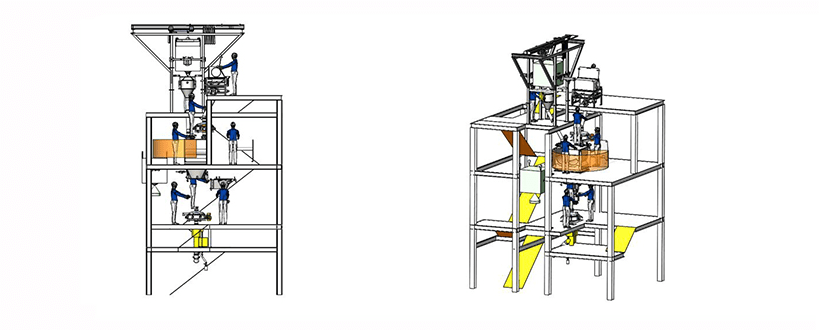
Why choose a DryMixFlow® mix line?
The knowledge of Palamatic Process’ staff in the handling of high value dry ingredients guarantees obtaining your desired results and will meet your expectations. The quality of construction of the hygienic equipment, coupled with a computer pilot of the line, ensures a high-quality end product.
Palamatic provides a single point of contact for your entire project and the monitoring of your production tool. Palamatic's after sales service department is available throughout the life of your production line with regular audits and IT updates, according to your manufacturing developments.
Contact our pre-project service dedicated to the world of ingredients to define in detail your DryMixFlow® mixing line.
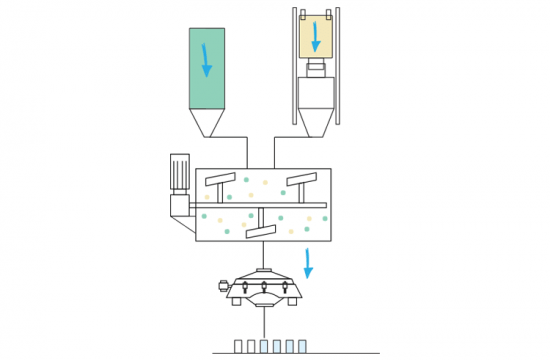
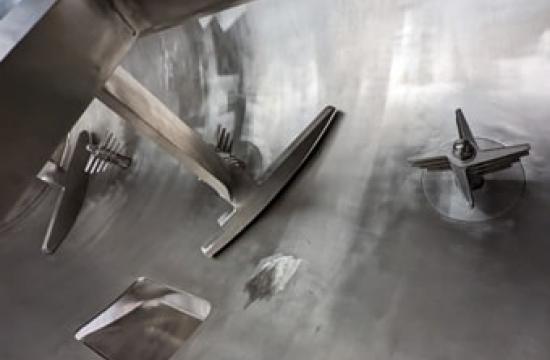
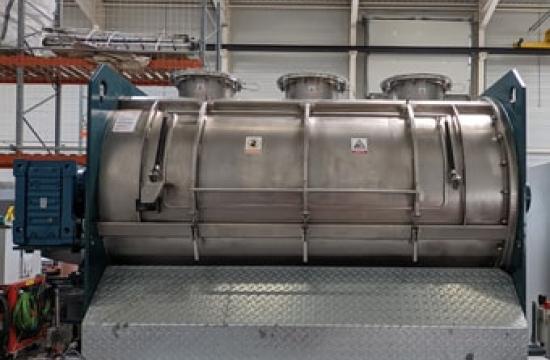
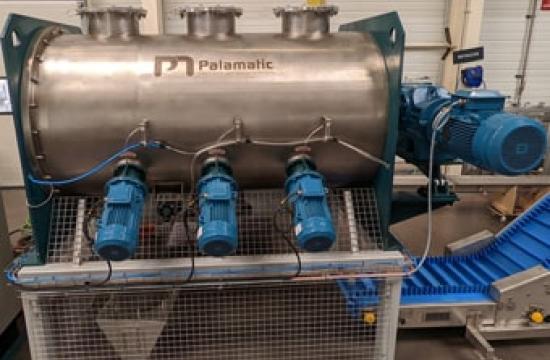
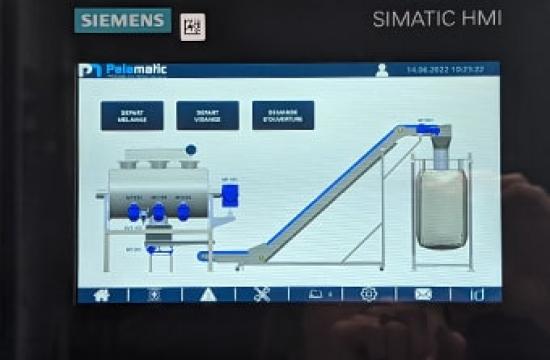
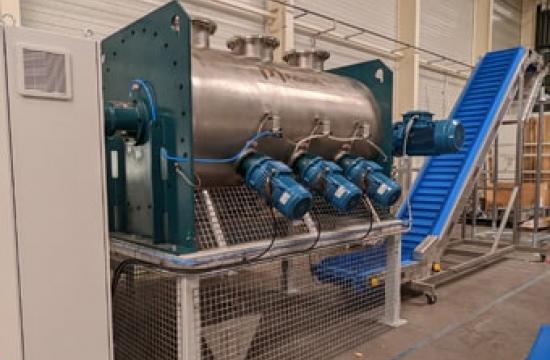
Discover the installations of our customers who use the mixing line dedicated to the DryMixFlow® dry mix.
All the equipment integrated into the DryMixFlow® process line is available below.