With recent economic developments, manual labor is more difficult to source then it has been in previous years. The need for industrial automation is on the rise as manufacturers look for new methods to decrease overhead and increase productivity. Palamatic Process offers automated bag splitters and material unloaders to meet this growing demand. But what distinct advantages does an automated bag dump station offer over a manual one?
1. Increased Productivity
With traditional bag dump stations, operators must spend a good portion of their shift lifting, loading, cutting and dumping sacks weighing anywhere between 10– 50 lbs. each. Manually, this process can be slow and tedious often resulting in 1-2 sacks per minute of material feeding into your process. This is not the best rate when end market demand requires an increase in production and material feed rates. Also, the repetitive carrying of loads leads to musculoskeletal disorders (MSD) for the operators.
Palamatic Process offers the “Minislit®” automated bag splitter, that can hit rates of 6-8 sacks per minute of material throughput, all in one contained system. * This heavy duty bulk material handling equipment can be used in the most difficult of material unloading operations. An assisted bag manipulator allows operators to keep up with the pace while eliminating the need to carry loads.
2. Less Operator Intervention
For the past several decades, the manufacturing industry has seen less demand for manual labor with the rapid increase in robotics and automated technologies. Furthermore, the labor market has shifted its focus towards other specialized skill sets including service, engineering, sales, marketing, etc. Many industries face increased pressure from global competition. As technology becomes faster and smarter, global markets become more accessible with better logistical and communication channels. By automating your industrial process, you minimize the impact of overhead costs and increase your responsiveness to pressure from global competition. The bag unloader Minislit only requires one operator for the entire station to load bags onto the conveyor, while the equipment does the rest (feeding, cutting, dumping, and waste removal compacting).
Palamatic Process can help you design a fully automated material handling systems whether its 25 lb. sacks or 1 ton bulk bags, our team has a solution for every application.
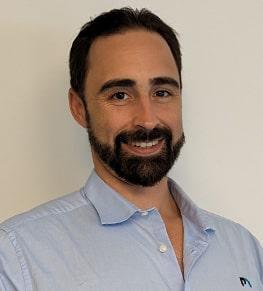
If your require further assistance,
I am at your entire disposal.
Tarik, powder expert
3. Operator Safety and Ergonomics
According to the Bureau of Labor Statistics, “Injuries and illnesses to manufacturing workers resulted in 32,470 DAFW cases of sprains, strains, or tears (28.0 percent); 16,790 cases of soreness or pain (14.5 percent); and 15,380 cases involving cuts, lacerations, or punctures (13.3 percent).” For an operator to repeat the same heavy lifting motion every day will eventually cause injuries such as back strains and shoulder tears. The safety of your workers should take precedence when planning an industrial process.
The Palamatic Process Minislit automated bag splitter is designed to minimize the need for operators to lift heavy loads in repetition. The bulk of the heavy lifting is conducted via vacuum lift, which makes the loading operation and discharging sack very easy to do. Our inclined belt conveyor takes away the risk of operators reaching, stretching or twisting while holding a heavy load.
By combining our vacuum lifter, belt conveyors and belt feed system, all the risky labor is eliminated to the operator. Our material handling equipment and conveyor systems make the most arduous tasks easy to accomplish.
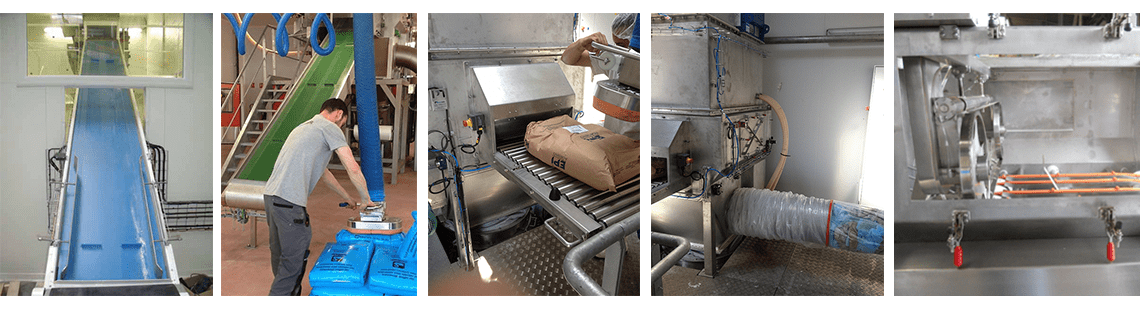
4. Dust Containment
Our team takes great care in the design of our automated sack unloading solutions. By minimizing powder retention areas and integrating suction filters (dust collectors), the Minislit® bagging equipment vacuum can fully contain dust emissions and bag waste. Our design team can integrate an independent dust filtration unit (independent dust collector) complying with ATEX standards for all your organic powders. Furthermore, for the automatic removal of dusty bag waste (paper, plastic, woven, etc.) a sack compactor is also built into the bag unloading unit. Once the ribbon saw makes its 3-sided cut on the bag, the patented inversion discs dump the material and feed the left-over waste to the sack compactor. The emptied bags are then compacted and contained inside a polyurethane sheath for sealing and removal by an operator.
Our team can further design our sack discharging station to meet ATEX and NEC regulations for explosion protection.
Since 1992, Palamatic Process has provided equipment to over 2000+ installations in over 30 countries. We offer knowledge and expertise in all manner of powder and bulk automated material handling needs. Examples include, conveyor systems: pneumatic or mechanical, pallet conveying, screw conveyors, roller conveyors, turnkey solutions, material flow devices, food-grade design, bulk bag equipment, etc. Contact one of our experts today for assistance with needed material handling solutions and to request a quote.