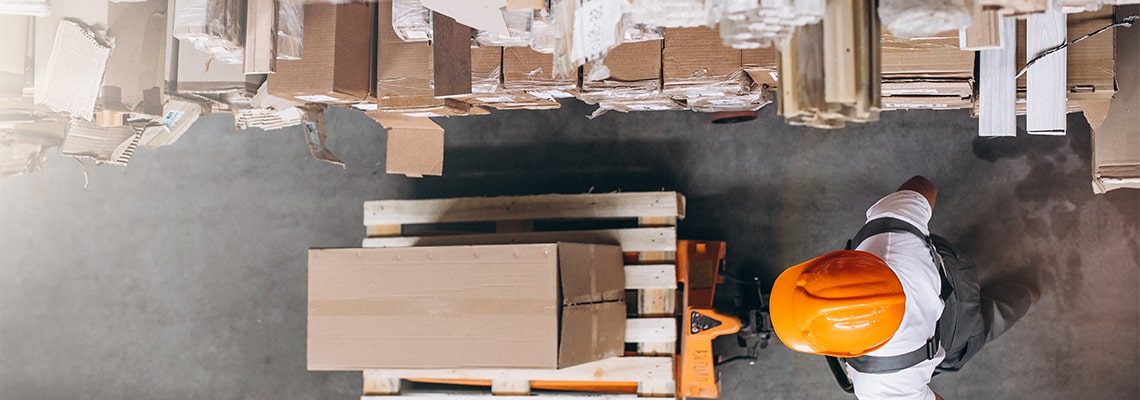
Musculoskeletal disorders (MSDs) account for 80% of work-related diseases. Almost all of these injuries are due to working conditions, in particular, manual handling. It is essential to know the safety criteria and recommendations to avoid any risk to production operators and enable them to work in the best possible conditions.
1. Definition of manual handling
According to the U.S. Department of Labor, handling is defined as:
Seizing, holding, grasping, turning, or otherwise working with the hand or hands. Fingers are involved only to the extent that they are an extension of the hand, such as to turn a switch or to shift automobile gears.
In this study, handling is considered as a production operator’s hands moving individual containers manually by lifting, lowering, filling, emptying, or carrying them.
There are several types and rates of manual handling.
Types of manual handling:
- Turning loads
- Lifting and setting down loads
- Carrying loads
Rhythms of manual handling:
- Isolated load carrying
- Occasional load carrying
- Repetitive load carrying
2. Thresholds limits
It should be noted that OSHA does not have a standard which sets limits on how much a person may lift or carry. However, the National Institute for Occupational Safety and Health (NIOSH) has developed a mathematical model that helps predict the risk of injury based on the weight being lifted and other criteria. The NIOSH model is based on previous medical research into the compressive forces needed to cause damage to bones and ligaments of the back. The mathematical model is incorporated in the Applications Manual for the Revised NIOSH Lifting Equation, which can be found on the NIOSH website. It should be noted, however, that this NIOSH document provides only voluntary guidelines.
The lifting equation establishes a maximum load of 51 pounds, which is then adjusted to account for how often you are lifting, twisting of your back during lifting, the vertical distance the load is lifted, the distance of the load from your body, the distance you move while lifting the load, and how easy it is to hold onto the load.
The difficulty with assessing risks associated with lifting is that weight alone does not determine the risk for back injury. Other factors include:
- How often you are lifting something.
- Whether you bend or twist while lifting.
- How high an object is lifted.
- Where the origin of the lift occurs; specifically, whether it is below knuckle height.
- Whether you hold the object away from you while lifting.
- How long you lift or hold the object.
Depending on these factors, an object that is safe to lift at one time can cause back problems another time.
While OSHA does not have a specific standard for manual handling and lifting, employee exposure to hazards related to heavy lifting and back injuries may be addressed under Section 5(a)(1) of the OSH Act, commonly referred to as the General Duty Clause. The General Duty Clause states:
“Each employer -- shall furnish to each of his employees’ employment and a place of employment which are free from recognized hazards that are causing or are likely to cause death or serious physical harm to his employees...”
If you would like more information on lifting hazards both OSHA and NIOSH have information on their respective websites which can be found at:
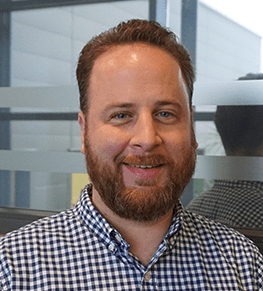
You have a handling project?
I am available to discuss the subject.
Chris, powder expert
3. Preventing MSDs
Several elements can increase the difficulty of manual handling. It is therefore important to anticipate them avoid any risk of MSDs. Among these aggravating factors, we find in particular:
- Related to the manual load itself: its weight, size, shape, height, distance travelled, etc.
- Organizational: high production rate, speed of execution, repetitive movements, night work, stress, etc.
- Workplace: surface area of the manual handling activity, slippery, cluttered floor, poor condition (e.g., fall hazard), etc.
- Ambience: cold or hot environment, lighting, etc.
An analysis of the risks linked to manual handling, training of personnel in the movement of loads, the provision of personal protective equipment (PPE) or the use of mechanical handling equipment are all measures that can improve the working conditions of operators.
4. Ergonomic equipment for carrying loads in industrial environments
Palamatic Process offers many solutions to reduce the risks of injuries and occupational diseases thanks to handling equipment adapted to different industries.
The industrial manipulators designed by Palamatic are intended for the handling of bags, drums, pallets, rubber blocks, cartons, etc. They use a vacuum lifting system that allows the handling of heavy loads (from 5 to 200 kg) without effort, which minimizes muscular fatigue. This equipment optimizes working time and reduces the risk of injury for production operators.
For filling and discharging stations of big bags, sacks and drums, Palamatic also has a range of ergonomic equipment ensuring minimum intervention requirements from operators, and a safer production process. The use of an electric hoist, a forklift or a low structure is also an integral part of our installations for loading bulk containers.
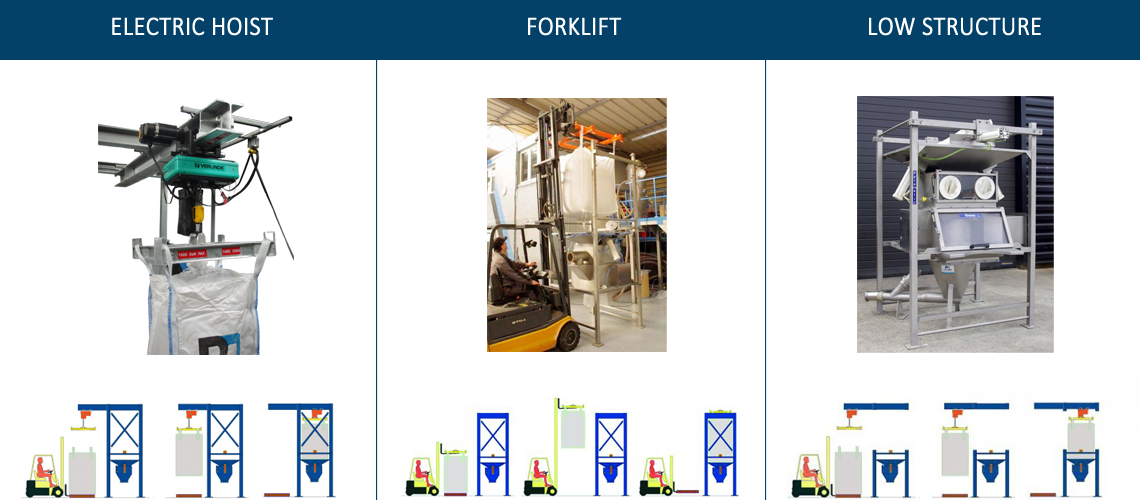
Discover our articles related to this topic: