Bulk bag filling system for the packaging of a pyroxene mineral consisting of lithium aluminum inosilicate.
Processed Powder: Spodumene
Our client, located in Canada, is a mining company dealing with minerals involved in the production of lithium batteries.
The goal of the project was to upgrade the packaging system with an automated solution for filling 1 ton bulk bags from an existing storage silo.
Production rate goals were to fill 20 bulk bags per hour with minimal operator intervention.
The Palamatic Process solution
After meeting with the client, our team decided the Flowmatic®04 bulk bag filling system would be the best solution for this project. Our client was able to provide buffer hoppers and screw conveyors for the transfer of the material to the automated FIBC filling station for the required production rates.
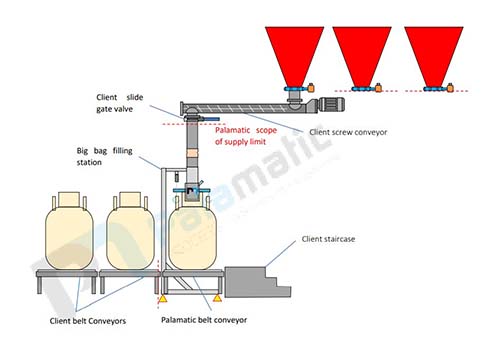
FIBC filling unit Flowmatic04©
To provide automation of the filling process and limit the need for operator intervention, the design starts with the bulk bag filling system. The operating objectives of this system include: filling bulk bags in automated sequence, contain dust emissions, optimize the filling of the FIBC and automated the sealing and evacuation of the bulk bag once filled. Capable of filling rates of 20-30 bulk bags per hour, the equipment integrates features such as: inflatable seal for dust containment, height adjustments for varying bulk bag dimensions, vibrating densification table, and bulk bag belt conveyor.
The operation cycle works in stages via the PLC system:
- The automated feeding of empty pallets via the pallet unstacker.
- The loading of the bulk bag on the automated hooking deck. - The inflation of the fill spout seal.
- The tensioning of the bulk bag to optimize its shape and reduce wrinkles or folds in the fabric.
- The inflation of the bulk bag by the pre-forming fan.
- The switch of the bypass valve to the balancing line connected to the vent or de-dusting unit.
- The authorization to open the material supply valve (or dosing equipment) above the filling station.
- The weight sensors (load cells) inform the controller of the filling weight of the bulk bag.
- Once the requested weight is close, the controls shut off the main flow valve.
- A "low speed" contact switches to a 4-20mA metering units for precise dosing.
- First vibration of the bulk bag for densification and stability.
- End of dosing, the tension cylinder of the bulk bag handles and the inflatable seal are exhausted to allow the evacuation of the bulk bag.
- The 2nd vibration for final densification and stabilization of the bulk bag.
- The belt conveyor evacuates the bulk bag to a buffer area for operator removal via forklift.
Due to the abrasive nature of the material, all parts in contact with it will be coated with a special type of rubber coating called Linatex. This product has an excellent resistance to abrasiveness as well as to wear and tear, it has a low permanent deformation threshold, and good elasticity properties allowing for easy application.
To further minimize the need for operator intervention on this line, as well as eliminate the need for an access platform structure, an automated sealing mechanism was integrated into the filling head of the station.
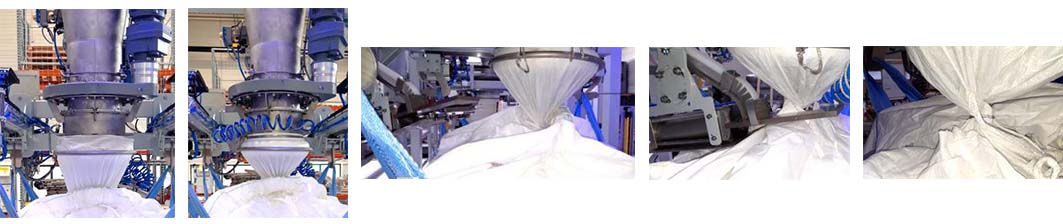
The electrical control panel interfaces with the system to provide automation of the filling, dosing, weighing, densification, sealing, release and conveyance of the operation. For this particular project, our customer preferred a Schneider Electric brand M251 MODBUS PLC and a 10” GTU touch screen interface.
Since 1992, Palamatic Process has provided equipment to over 2000+ installations in more than 30 countries. We offer knowledge and expertise in all manner of bulk powder handling equipment solutions. Examples of our equipment offerings include: conveyor systems, bulk process equipment, pneumatic conveyor systems, dust collection, and bulk handling systems. Contact one of our experts today for assistance with needed material handling solutions and to request a quote.