Description
AUTOMATIC BAG DUMP STATION - VARISLIT® - For high speed deconditioning, multi bags from 15 to 50 kg without adjustments
Automatic bag dump station with double-blade rotating system for processing large bags with an extremely high emptying rate without dust emission into the atmosphere.
The Varislit® bag opener is widely used in the food, pharmaceutical, chemical and agrochemical industries. Its patented inversion system conveys empty bags in a screw compactor, which is an integral part of the system. The dust extraction option offers the best solution for fast, dust-free automatic opening. The double-blade rotary system, which is standard on this machine, and its elongated shape allow to handle large bags with an extremely high emptying rate. The entire mechanics are placed outside to avoid contact with the material (bulk, powder...).
This machine is designed to open 12 bags/min.
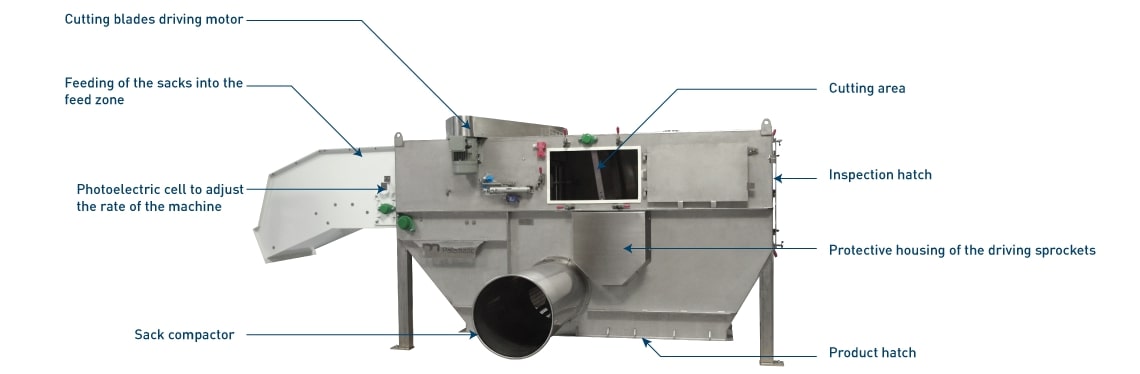
-
Rate5
-
Overall dimensions4
-
Hygiene4
Operating mode
1. The operator positions the bag with a bag manipulator on the belt conveyor that supplies the bag dump station
2. The bag is detected by the sensor controlling the cutting system
3. The blade cuts the bag and the lower part is grasped by the inversion discs
4. When the sensor is deactivated, the blade returns to the rest position so as not to cut the bag in half
5. The bag is then directed to the bag compactors and the machine is ready to receive the following bag
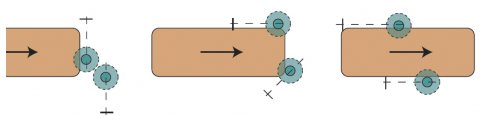
Synoptic of bag turning
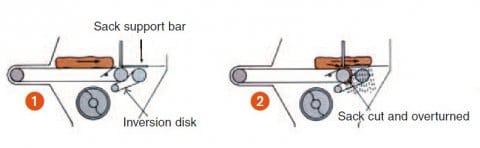
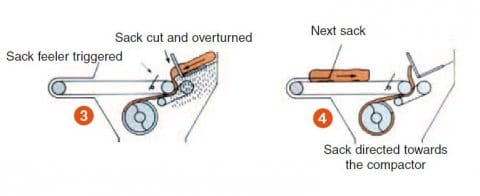
Equipment advantages
- Suitable for a large number of types of bags: paper, polywoven, lined...
- Minimizes handling by the operator
- Increased productivity
- Reduction of dust emissions
- Integrated bag compactor
- Easy to clean
Media
View our equipment in videos
Dessacheuse automatique Varislit
Vide sacs automatique
Cette dessacheuse permet l'ouverture automatique avec un respect des produits fragiles et un encombrement machine réduit.
Dessacheuse automatique
Cette machine garantit un travail dans un environnement sans poussières et sans nécessité de découpage manuel des sacs.
View our equipment in photos
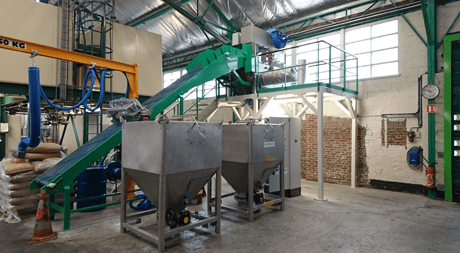
Automatic sack discharging
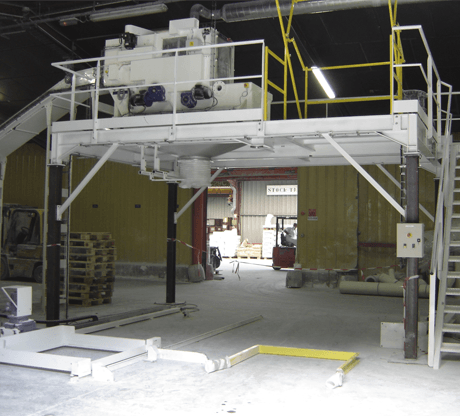
Automatic sack discharging with platform
Implementation of an automatic bag discharger for the treatment of plaster for the building industry.

Automatic bag dump station
Cement deconditioning with pneumatic conveying.
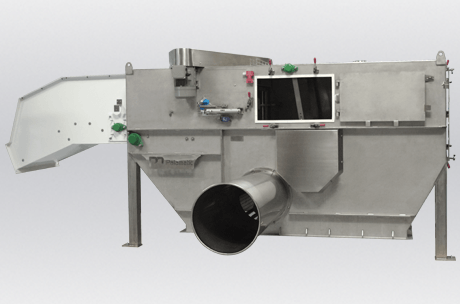
Automatic bag dump station - Varislit
High speed multi-bags deconditioning.
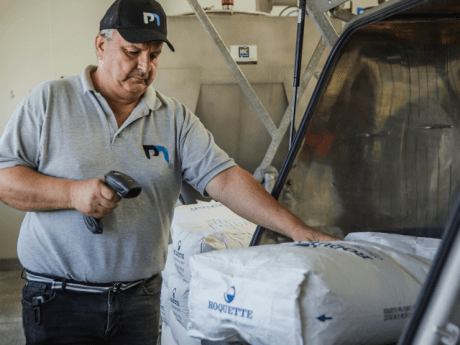
Bag tracking
Batch tracking for the protection of your process.
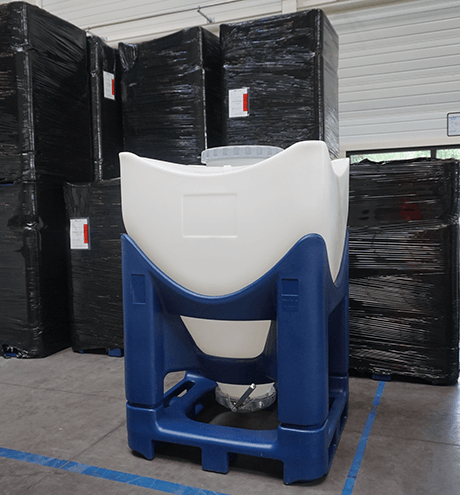
Automatic bag dump station high rate
The operator lifts the bag using the bag manipulator. The bag is then discharged into the emptying station. Finally, the powder is hygienically transferred into the storage container.
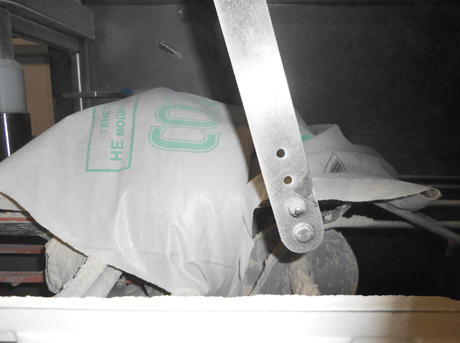
Automatic sack discharging
Interior view of the Varislit® with the cutting system and the compaction screw.
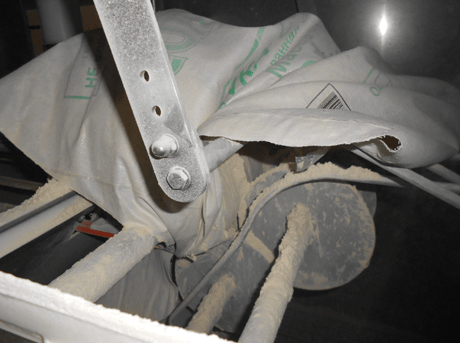
Powder processing automatic sack unloading
The holding roller can be used to process bags weighing less than 15 kg.
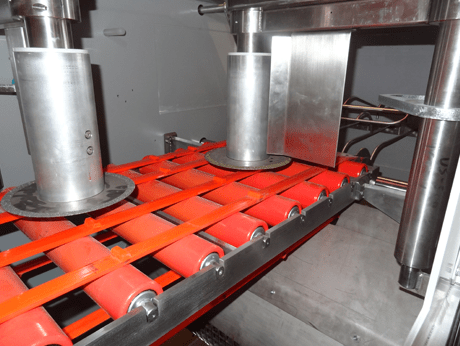
Automatic bag dump station internal view
Very high speed bag discharging station.
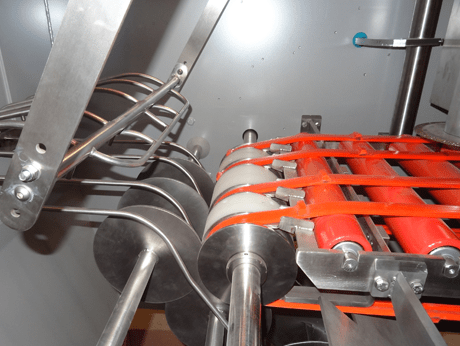
Automatic bag dump station internal view
Feeding of a reactor with a sieve.
Features
Technical specification
Capacity | 15 to 50 kg/sack |
---|---|
Manufacturing materials | Painted steel, 304L stainless steel, 316L stainless steel |
Electrical power | 7.5 kW |
Pneumatic consumption | 2 Nm³/h. |
Dust removal rate | 600 m³/h. |
Electrical powers | |
---|---|
Bag suplying conveyor (optional): | 1.5 kW |
Cutting head drive motor: | 1.5 kW |
Compactor and internal conveyor: | 2.2 kW |
Fan motor (optional): | 1.5 kW |
Vibrating motor (optional): | 0.25 kW |
The machine is supplied with a complete control cabinet to ensure the desired output.
Dimensions
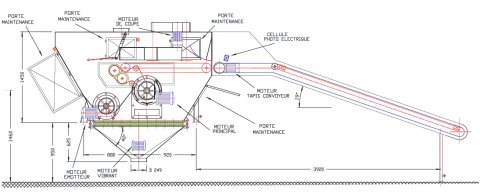
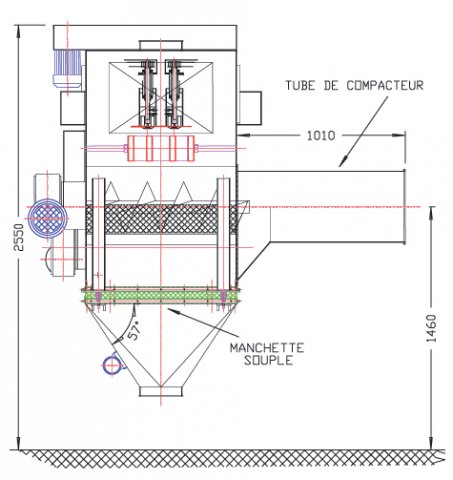
Options
Case studies
CASE STUDIES WITH THIS EQUIPMENT
Plaster preparation
Processed powders: plaster, cement and starch - Plaster preparation - Leading company in the manufacture of plaster and plasterboards. The objective of this installation is to empty 25kg bags at high...Minerals and building
Tanning product
Processed powders: chemical additives - Tanning product - The great diversity of the products and their varied packaging meant that this plant had long been looking for a system that would reduce the...Chemical
Oil drilling muds
Processed powder: barite - Oil drilling muds - Company working in the treatment of drilling muds. Barite, high density and abrasive material, is used as a binder in drilling muds to facilitate the...Chemical
Drinking water filtration
Powder processed: activated carbon and lime (with a respective bulk density of 0.5 ton/m³ and 0.6 ton/m³) - Drinking water filtration - The customer requires a pneumatic conveying system, at a rate of...Water and smoke
Premix for coating
Processed powders: PVC powders - Premix for coating - This installation involves a manufacturer of coated fabric. Coating is a surface treatment that consists in applying a layer on a substrate (paper...Chemical