Processed materials: citric acid, potassium sorbate, sodium benzoate...
Loading of ingredients for the production of soda
This installation concerns a new production line in a new building of an existing factory.
The main objective of this installation is firstly to automatize the filling of big bag of premix, ensuring the cleanability and the absence of product retention to avoid cross-contamination.
All equipment (except electrical hoists) are mounted in a ATEX 21/22 area. All contact parts with product get a mirror polish finish, in order to get a minimum retention and optimize the flow of the product.
2 big bag discharging station EasyFlow® EF0 and 2 big bags and sack discharging stations are located on the 2nd floor. Several ingredients are discharged from these stations either stored in big bags or in sacks. The big bags are loaded on the structure thanks to electrical hoists. The opening of the big bag is done thanks to a dustproof docking system with an active/passive cone system to ensure a healthy working atmosphere.
Indeed, these 4 stations are fitted with a cone valve that is fully automated. Partial discharging of big bags at any time and in a dust-tight manner is made possible through the use of these cone valves.
The 2 discharging stations designed for sacks and big bags are each fitted with a mobile hopper that allows the dumping of the ingredients contained in sacks. This hopper can therefore be easily removed when it comes to emptying big bags. The active/passive cone system is also used here.
The 4 stations on the 2nd floor are equipped with lump breakers that are positioned on mobile frames. This lump breaker EC35 is fitted with a flexible fitting upstream and downstream so that the different parts can be easily removed for washing and can be changed between the various bulk materials handled.
When we reach a “low speed” feeding, the required weight is reached, the active valve progressively closes, in order to control the accuracy to reach the target weight.
On the 1rst floor, 4 docking stations are positioned under each discharging station. These docking stations are used with IBCs and are connected with the discharging station on the upper floor thanks to pipings with internal sheath that can be changed between products to avoid cross-contamination. The IBC discharging stations IBCFlow® are equipped with a vibrating table, in order to help the flow of the product into below equipment.
These industrial containers are then completely discharged into big bags using a semi-automatic big bag filling station FlowMatic® 04 located on the ground floor. The empty pallets are stacked on a pallet unstacker. The conveyor under the filling frame is weighed.
This big bag filling station can also be used to fill drums or plastic bins thanks to switchable filling heads. Once filled with the premix, the big bags are removed using a roller conveyor and an operator with a forklift can remove the big bag to bring it to the storage area.
All the stations are connected to a centralized dedusting system to ensure to work in a healthy atmosphere.
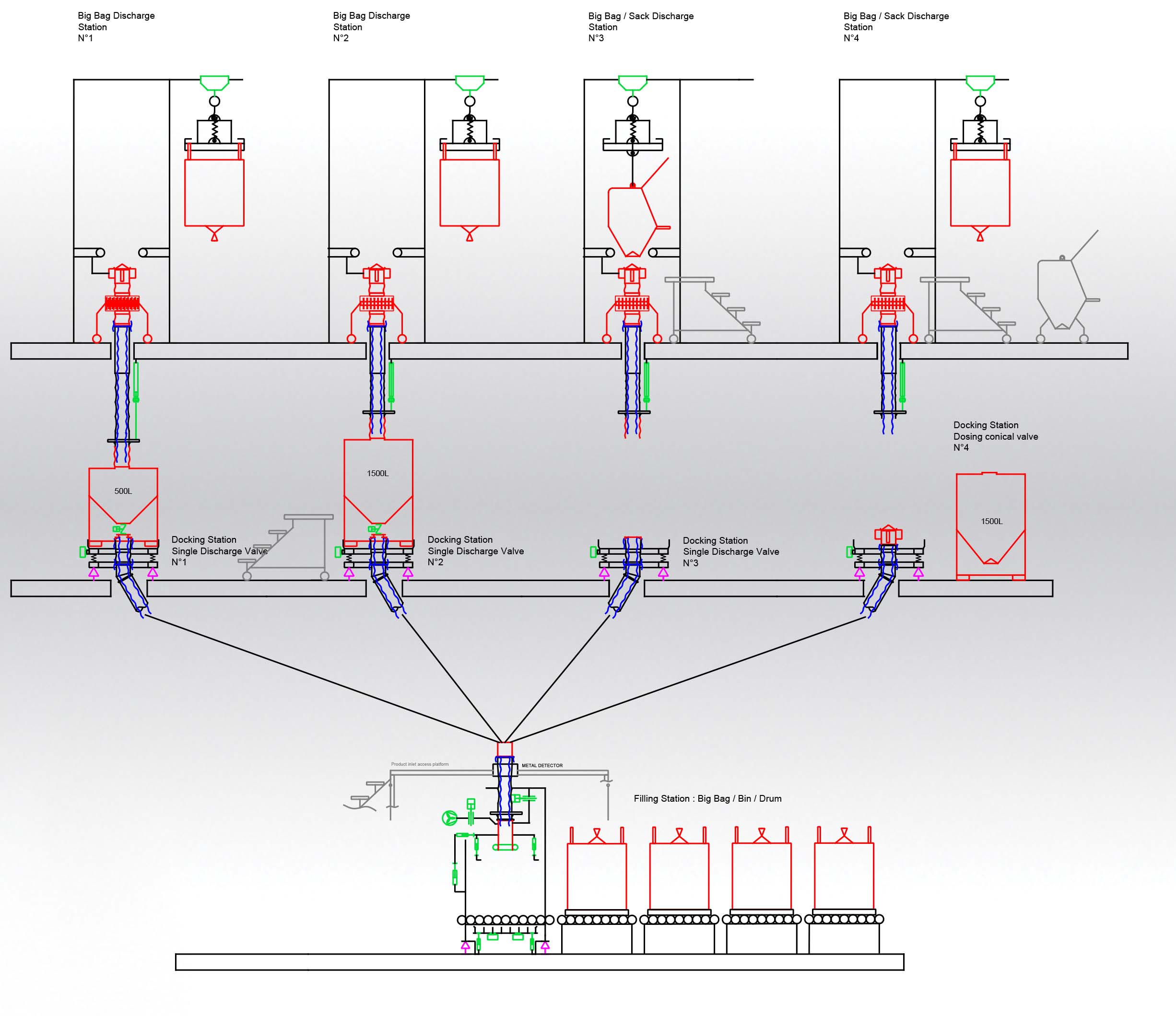
Process diagram