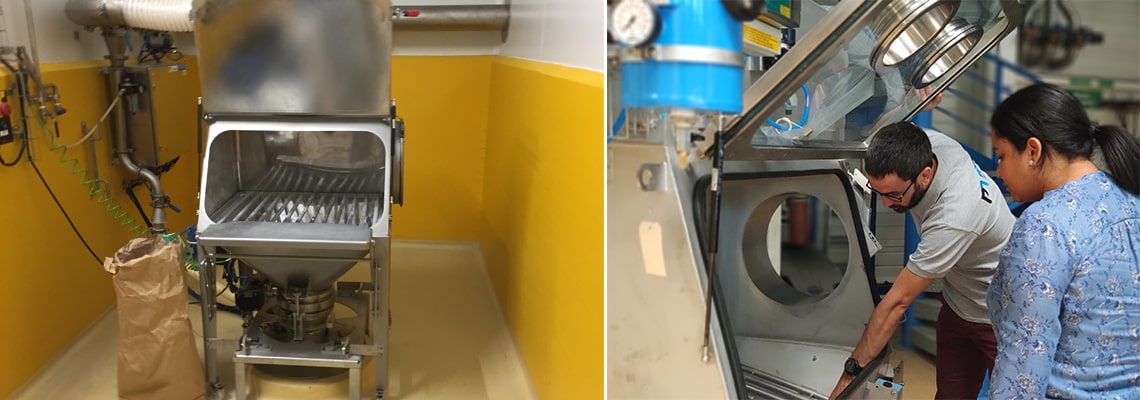
Dry bulk solids are stored and shipped using a myriad of packages and containers. Pails, buckets, drums, bulk bags and boxes are all very common methods when it comes to manufacturers delivering bulk materials to their clientele. One of the more common practices is using 50 lbs. to 75 lbs. sacks containing different dry ingredients and powders. Often made of either a polyethylene or paper material, they are easy to stack and unstack on pallets for bulk transport. However, these bags of powders and bulk solids can be more labor intensive, often requiring an operator to manually lift, cut and dump the material into a production process. Several industries use this method of powder delivery including chemical, food & beverage and minerals to name a few. Bag dump stations (also called sack tip trays) are a common piece of equipment found in many dry powder production facilities. They help provide a place to rest the bag for the operator to cut and pour the material into the downstream process.
Bag dump stations often can be very simple in construction, offering a grate to rest the bag on, a hinged door for access, and a hopper with a flange to help funnel the powder into production. However, many options and features are available to help meet the specific demands of different types of manufacturing lines. Before buying a bag dump station you should ask yourself the following questions.
1. What is the risk of exposure to the operator and what level of containment should you plan for?
Some powders can be potentially harmful to an operator’s respiratory system, or may contain toxic carcinogens. Your equipment provider should be able to offer a few solutions to prevent and safeguard the health of your workers.
Glove Box style designs can help keep a physical barrier between the powder discharge operation and the operator. This type of setup typically utilizes a side manual roller feed with flap door to help stage the bag inside the station. Once inside, the operator can use latex or nitrile gloves that are integrated into the see-through front window. The operator is therefore fully protected from exposing themselves while they have that barrier in place for cutting and dumping the powder material.
You may have concerns about good housekeeping and minimizing the dust that can get into the atmosphere of your facility. Many powders can have very light bulk densities which means particle can become airborne much more easily compared to those with heavier bulk densities. Sack tip trays can often either provide a tapping for connection to an existing central bag house, or, a complete jet pulse dust filtration system built into the unit itself. Integrating a dust filter is a key component to designing a powder discharging station to be dust tight in operation.
What do you do with the empty bag once the powder has been unloaded into the production process? A common practice in many production plants is to simply discard the open bag into a waste receptable and physically smash them down as the bag waste begins to build and take up space. Bag compactors (sack compactors) can further enhance your ingredient unloading methods by providing a safe and contained method for getting rid of empty bag waste. Compactors can be integrated directly into the side or back of a bag dump station, or, be offered as a stand-alone solution.
2. Does your material contain lumps or have poor flow properties?
Bags that have been transported over long distances are often compressed by the time they arrive at their destination. Furthermore, the powders could have been exposed to moisture or humid conditions. This will often times cause the powders inside the bags to form soft and/or hard agglomerates that may need to be broken up before feeding into your production process.
One option to consider is a vibrating screener (also called vibratory screeners or flat deck screeners) which consists of a circular mesh screen and an external vibrating motor. The motor can be adjusted to intensify the vibration and ensure good flow of your powder through the screen mesh. They can be designed for quick assembly and disassembly for cleaning in sanitary and hygienic production processes.
Another common option is integrating a lump breaker directly below the discharge outlet of the sack tip tray. Lump breakers (also called lump crushers, granulators or flakers) are commonly designed with an external motor, housing unit, rotating teeth and a fixed grid for basic classification of the lumps. The rotating crushing medium impact the solid lumps of powder against the fixed grid, causing the agglomerates to break apart back to their natural granular state.
If your powder material is sticky, bridges or just has bad flow properties in general, flow aid devices can be mounted on the discharge hopper of the bag dump station. There are many types of flow aids but common examples include: pneumatic turbine vibrators, pneumatic roller vibrators, bin aerators and anti-bridging devices. In most applications, externally mounted vibrating flow aids are used to help shake the product off the surface of the hopper, and aid in the emptying of the bulk solids into the downstream process.
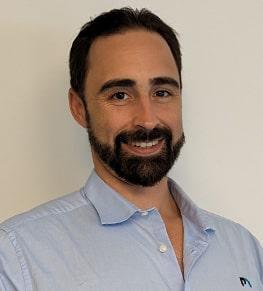
Do you have a project? I am available to
advise ou and accompany you in your study.
Tarik, powder expert
3. What are your production goals?
Or more specifically, how many 50 lbs. sacks do you need to unload per hour (or per minute) of production? What level of automation do you require for your production process? What if you need to unload your materials at a rate of 6 sacks per minute?
One operator with one bag dump stand will not be capable of that high of a production rate. Certainly, many production plants may opt for six bag unloading stations with six operators manning those stations.
Another alternative is semi-automated (Ergotip®, SAS) or fully automated bag splitting equipment (Minislit®, Varislit®, Rotaslit®). Equipment suppliers can offer varying degrees of automation to assist an operator with unloading sacks of bulk powders. Some semi-automated sack tip trays may offer a clamping device to hold the bag in place while a pneumatic blade punctures the bottom of the bag. Pneumatically actuation folding arms can then fold the bag in half to help discharge the material contents from the bag. Fully automated versions might include a belt conveyor or roller conveyor to feed the bags into a cutting chamber. Once the bag is inside the chamber, sensors will detect the bag and actuate a cutting device (for example a band saw) to partially cut the bag open. The bag is flipped over, spilling its contents, and then conveyed to an integrated sack compactor for automatic waste removal, containment and compaction for volume reduction. Robotic depalletizing arms can also be used to help load the bags of powder onto the motorized belt conveyor for full automation with no operator intervention needed.
Depending on the type of powder and bag, many automated bag opening systems can reach rates of 6-8 bags per minute per station.
4. What other options should be considered?
Vacuum bag lifting equipment is another supporting device that will help operators reduce the repetitive strain of lifting heavy bags of powder. Also called bag manipulators, they work on the principal of vacuum suction that holds the bag in place on the sealing foot of the equipment. By increasing or decreasing the amount of suction, the operator can lift and lower the bag with minimal effort. Vacuum lifters often comprise of a vacuum pump, adjustable hoses, lifting and lowering handles, and a floor or wall mounted jib crane that can swivel on its axis. Furthermore, these vacuum lifters are often adaptable to various types of containers with a quick change of the suction boot (i.e., drums, pails, boxes, rubber bales, pallets, etc.).
What if you need to transfer the bulk material to a hopper or mixing equipment downstream? Screw conveyors are commonly used on the outlet of the sack tip tray to move the unloaded material to the next stage of your process. Rotary valves and pneumatic conveying systems can also be integrated into the outlet end of the bag dump station.
What if your process requires unloading bulk bags for major ingredients (like sugar and salt) and minor ingredients in 50 lbs sacks? Equipment suppliers can integrate a combined bulk bag and sack unloading station in one unit. The bulk bag can be hung over the support tray it rests on while an operator can access the untying box that also doubles as a sack tip tray. Two unloading methods in one product stream.
Contact one of our experts today for assistance with needed material handling solutions and to request a quote.