Processed powders: wheat bran and lime with a bulk density of 0.4 to 1 kg/m³
Wheat bran and lime premix line
Our Client: an engineering company that specializes in the design of industrial operations for the agri-food and animal nutrition industries.
The end-user’s goal was to produce premixes at a throughput of 2,000 tons per month for a first production campaign dedicated to animal protein and a second dedicated to herbal raw materials. The raw materials are delivered in bulk bags and sacks and the customer required a flexible installation to ensure integration into the industrial production line.
Big bag emptying station with untyingbox
Palamatic Process supplied an EasyFlow® EF01 bulk bag discharging station to allow the bulk bag to be loaded using an electric hoist and handling cross. In order to facilitate the flow of bulk material, silent-blocks and a 0.1 kW vibrating motor are integrated into the deposit tray for vibration effects. The operator opens the unlacing cabinet and unties the bulk bag spout to allow material discharge. Four pneumatic massage cylinders apply pressure to the lower and lateral parts of the bulk bag to facilitate the flow of the bulk material, which can form lumps.
A EC35 lump breaker is positioned at the outlet of the bulk bag discharging station to break up any lumps in the product. Eight blades are mounted asymmetrically on a very high-strength shaft which is driven by a motor gearbox with high torque. This design can reduce very hard agglomerats to a size acceptable for pneumatic conveying.
Bulk bag and sack discharge station
In parallel with the EasyFlow® EF01, Palamatic Process provided a station that allows the unpacking of both sacks and bulk bags. This two-in-one unloading station is the Duopal® DP11 model. This solution provides the required flexibility the customer required to balance out recipes, if needed, by adding a sack or a bulk bag when the EasyFlow® EF11 bulk bag emptying station is in operation.
The bulk bags are loaded using an electric hoist, and once in position on the dispensing tray, the operator unties the spout via the unlacing cabinet. As an option, the unlacing cabinet can be designed as a glovebox so the operator has no direct contact with the bulk material being handled. The self-supporting structure is adjustable in height to accommodate various bulk bag sizes. The telescopic connection tube allows a completely sealed connection between the bulk bag and the discharge station.
To optimize the flow of the bulk materials (even compacted ones), four massage cylinders are installed on the lateral and lower parts of the bulk bag and massage the flexible container for total emptying.
The operator manually places the sack on the dispensing table and positions it on the screen above the powder discharge hopper. Once the sack is cut open, the operator shakes the bag to empty the powder and evacuates the empty sack through the built-in compactor. The bag compactor compresses the bags through a helical screw and discharges them into a polyethylene sheath. The access door to the station is equipped with pressurized springs to allow secure locking in both the open and closed position, as well as facilitate its opening.
An EC35 knife lump breaker is located at the outlet of the bag dump station to de-agglomerate the bulk material lumps.
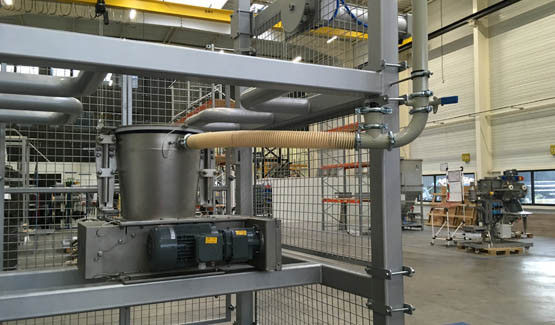
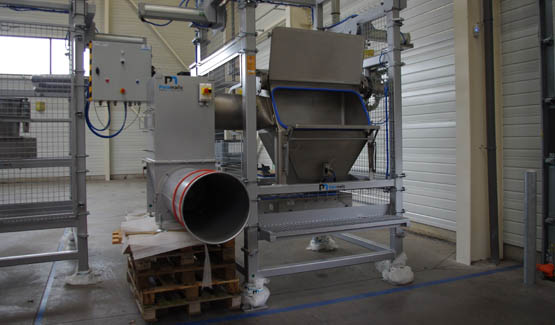
Dust removal system
The two bulk bag unloading stations are connected to a dust collection unit, with a flow rate of 1,500 m³/hour, installed outside the factory. This dust extraction system maintains a healthy working atmosphere, without pollution and without product loss.
Feeding of storage hoppers
Once the bulk materials are transferred through a tubular screw, they are conveyed to four storage hoppers that contain the premixes before industrial mixing and packing operations are carried out.
Bulk bag filling
The customer operates two packaging lines for the premix in bags. However, anticipating future production requirements, they wanted to add a bulk bag filling station. Palamatic Process therefore presented the FlowMatic® 02 bulk bag filling station. This station is simple and robust and is designed to fill between 10 and 20 bulk bags per hour. The operator places the bulk bag on the packing station by connecting the filling spout to the inflatable seal and clamping ring. These features provide dust containment and high filling rates. A pneumatic cylinder, positioned on the upper part of the structure, raises the bulk bag for tension and optimal filling. Once these operations have been carried out the filling of the bulk bag can begin. Once finished, the seal deflates and the bulk bag is ready to be removed. The U-shaped forks of this bulk bag filling station are adjustable in width to allow optimal filling of all types of bulk bags.